Get the industry’s most precise assembly failure detection solutions for medical device manufacturing
Medical Device Leak Testing
When it comes to the development and manufacture of medical devices, product leakage could cost a person’s life. Accurate, reliable leak testing solutions are critical for mitigating risk, containing R&D costs, and complying with 21 CFR Part 11 EU Annex 11.
CTS offers instruments to address a range of test methods and requirements. With our Sentinel line of leak testers, we’ll help you accurately and reliably test medical devices such as catheters, tubing sets, and fluid bags for leaks or blockages. We also provide customizable systems for benchtop or automated assembly operation, while meeting the specific testing requirements for your medical device.
High Precision Testing for Disposable Medical Devices
What sets CTS apart is our extensive knowledge of regulations and industry-accepted equipment testing guidelines for medical device testing, including applications, process validation, data collection and storage, calibration, and test specifications. Because every customer is different, we provide reliable medical device leak testers that can be configured based on your exact needs.
We work confidentially with partners ranging from global corporations to small, specialized startup ventures. Our team has extensive experience in testing equipment and will work with you to develop a medical leak testing solution that is specifically tailored to your unique needs.
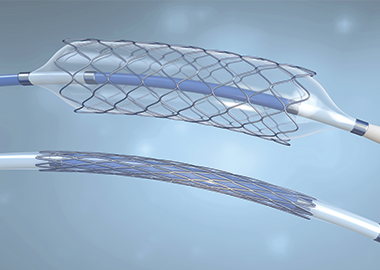
Cardiovascular Devices
CTS offers many testing options for cardiovascular devices, including leak test devices for balloon catheters, multi-lumen catheters, and vascular access sheaths.
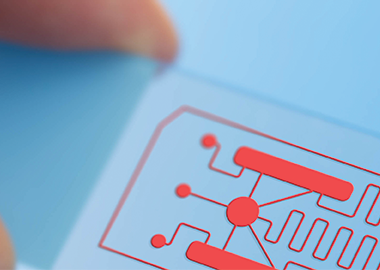
Diagnostic Sets
In diagnostic applications, such as microfluidic chips or reagent cartridges, CTS leak testers reliably detect leaks and blockage.
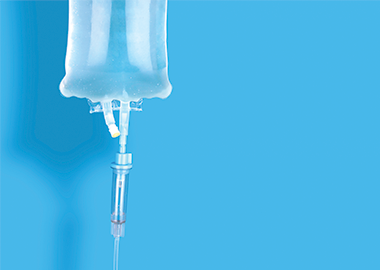
Solution, Drug & Blood Management
CTS has extensive experience in leak testing products used to manage liquids, such as bags, cannula and flow regulation devices, check valves, and tubing sets.
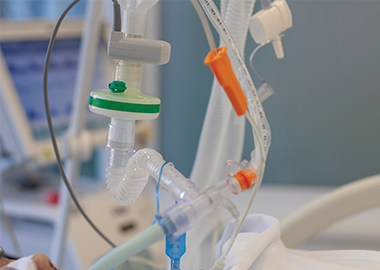
Respiratory Devices
Mass flow testing is often used to address the numerous configurations of respiratory devices, such as breathing circuits, humidification chambers, nasal cannula and more.
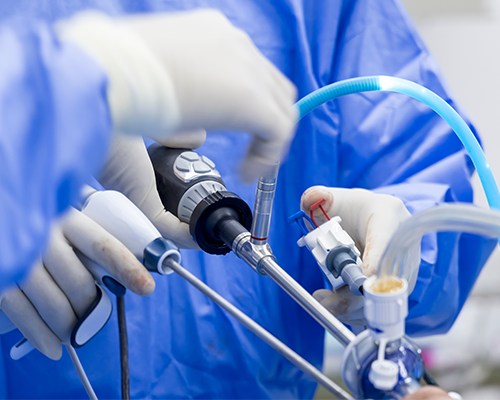
Endoscopic Devices
CTS has the expertise to ensure accurate and reliable leak and blockage testing of disposable laparoscopic/endoscopic devices, which require precise testing processes to accommodate complex device structures and multi-seal systems.
Trusted Leak and Blockage Testing for Medical Devices
The trend toward personalized medical care has also driven a demand for precision medical devices. No longer a one-size-fits-most industry, many types of medical devices now come in a wide range of sizes and features, along with complex geometries like as tubes, balloons, bags, and other components that can make testing more challenging. Variables like flexibility and elasticity of common polymer-based disposable medical device materials can have a significant impact test repeatability.
To address these complexities, medical device leak testers must provide effective sealing and understand how to deliver and measure the pressure with adequate sensitivity to produce accurate test results. Part of this includes selecting the optimum medical leak testing method and equipment. With years of experience in the medical device industry, CTS’s team of application experts will work with you to identify the best leak testing solution for your specific needs.
Leak Testers, Seals and Turnkey Systems for Medical Device Manufacturing Quality
CTS Sentinel Blackbelt and Blackbelt Pro instruments feature technology that provide greater measurement precision and accuracy—up to 6x more compared to other systems. We also offer automated, turnkey leak and flow benchtop system for medical devices. When superior sealing is required, particularly for catheters and small valve assemblies, we provide Luer connectors for a durable seal.
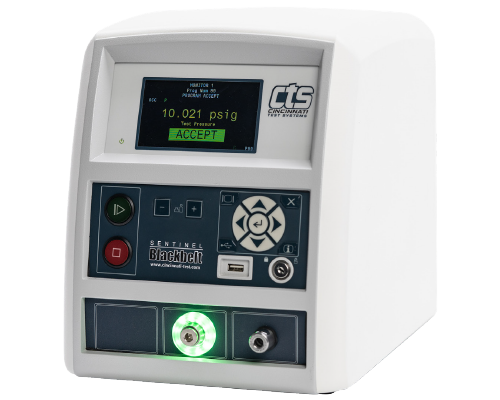
Sentinel Blackbelt
The world’s most versatile single-channel pressure decay and mass flow testing instrument. A high-precision benchtop instrument, it provides unmatched flexibility in a proven, standard platform.
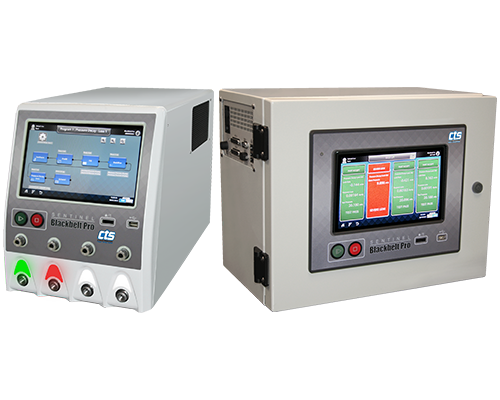
Sentinel Blackbelt Pro
Multi-channel leak, flow, pressure, and vacuum instrument available in wall mount and benchtop configurations. 21 CFR Part 11 & EU Annex 11 friendly, it provides up to four individual testing channels with one fully integrated instrument.
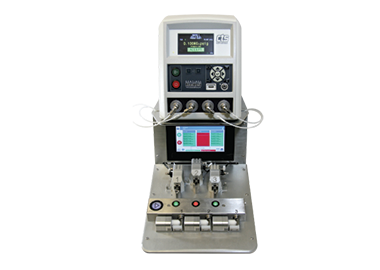
Turnkey Leak and Flow Benchtop Test Systems for Medical Devices
Automate your leak testing with a turnkey test solution fully controlled by a Sentinel Blackbelt instrument.
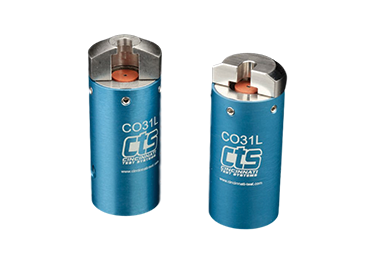
CTS Connect with Luer Connectors
Our CTS Connect product line offers luer-style connection fittings for use in the medical industry and a range of other options to seal parts during test.
What is the Difference Between Pressure Decay and Mass Flow Medical Device Leak Testing?
Pressure decay testing involves pressurizing the component and then isolating it from the pressure source. If a leak is present, the air will move from a high-pressure area to a low-pressure area, resulting in a decrease in overall pressure that is then measured by the equipment.
Mass flow leak testing involves pressurizing the component and then monitoring the amount of air flowing into the part. The medical device leak tester then detects the presence of a leak by measuring how much air is required to maintain the internal pressure.
The higher the volume of air required, the larger the leak. Our application engineers will work with you to determine the best solution for your unique requirements.
On-demand Webinar: Intro to Leak & Blockage Testing of Medical Devices
Learn the fundamentals of leak testing and the most common methods used for medical devices.
Contact CTS
To Discuss Your Leak Detection System Requirements
Contact CTS
Contact Cincinnati Test Systems to learn more about our leak detection equipment
Contact UsCustomer Login
An account is needed to view restricted documents such as user manuals and to submit RFQ requests.
Sign In