Vacuum Leak Test Systems
Leaks, even when they are small, can have a significant impact on the performance of a part or component or cause equipment to fail. Cracks and faulty seals are often the cause of these leaks, they can often be detected by conducting vacuum testing on components prior to manufacturing.
Using a vacuum leak tester is the principal leak test method for testing sealed parts that could have leakage from an external source into their housings and casings. Prime candidates for vacuum leak test procedures include:
- Electrical sensors or housings that can be affected by atmospheric pressure changes
- Outdoor electrical housings
- Sealed components
- Components associated with vacuum sources
Is There A Difference Between Vacuum Leak Testing and Pressure Decay Testing?
Vacuum leak detection functions in a similar, but essentially opposite, manner as pressure decay testing. During a pressure decay test the part is pressurized with dry, clean compressed gas (dry Nitrogen or shop air). During this fill cycle pressurized gases heat up, requiring a stabilization period necessary to dissipate the heat for stable leak testing. During a vacuum decay test, a regulated vacuum source is applied to the part, any thermal event that occurs during this operation is highly reduced and requires less stabilization time prior to conducting the leak test cycle.
Compared to pressure decay testing, vacuum leak testing can provide better repeatability as it is less sensitive to environmental variables created by temperature changes. A vacuum leak detector often requires less time to reach a stable test pressure, is less susceptible to potential instability of tested parts, and offers shorter cycle times than tests in many pressure decay applications.
The other difference between pressure decay and vacuum decay testing is related to the pressure differential that is created across the leak path and forces created on the part. When conducting vacuum decay testing, the greatest differential that can be created is related to atmospheric pressure and typically vacuum decay testing is not conducted at full vacuum. Pressure decay testing, however, can create a much greater differential across the leak path because of the ability to use compressed gases (caveat: the higher the pressure, the longer the stabilization time required).
When extremely high pressures are needed to conduct a pressure decay test, CTS suggests conducting a vacuum decay test on the part placed in a test chamber, the part is pressurized with high pressure and vacuum is applied to the test chamber as a vacuum decay testing is conducted. This technique allows the thermal event to occur within the part but does not affect the outside vacuum chamber leak test to accommodate repeatable testing results.
Our Vacuum Leak Test Solutions Provide Accurate Testing and Reliable Results
Cincinnati Test Systems (CTS) designs and manufactures a full line of vacuum leak test instruments that utilize innovative technology to deliver reliable, repeatable solutions to leak testing challenges. We differentiate ourselves from the competition by offering a broad range of vacuum leak test technologies that can be seamlessly integrated into custom turnkey systems.
Contact CTS to learn more or to request a quote on the vacuum test instrument you need.
Turnkey Vacuum Leak Detectors Configured to Your Specifications
Effective vacuum leak test procedures require more than just a vacuum test unit. We offer a full line of state-of-the-art vacuum leak test instruments that feature proven mechanical designs and superior engineering for fast test cycles and consistent, reliable results. If you need a complete vacuum leak detector system, look no further than CTS.
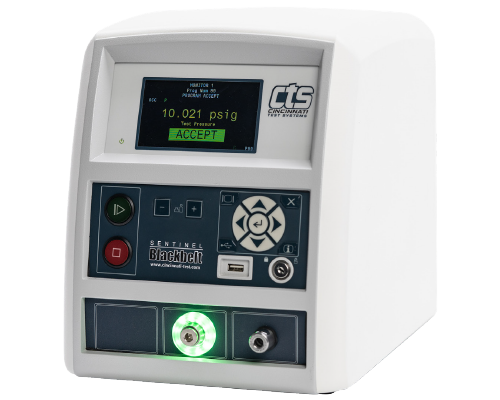
Sentinel Blackbelt
A multi-test configurable vacuum leak tester solution with a benchtop configuration. Features auto setup and calibration and standard test pressure ranges of -14.5, -2, 0.5, 2, 10, 30, 100, 200, 400, 500 or electronic regulation (PSIG).
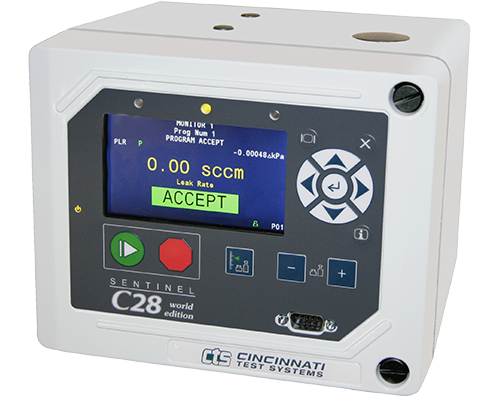
Sentinel C28WE
Single test configurable vacuum testing in a wall-mount configuration. Features auto calibration and adjustable environmental drift correction. Standard test pressure ranges are -14.5, 2, 10, 30, 100, 200, or electronic regulator (PSIG).
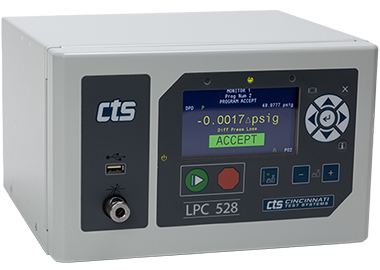
Sentinel LPC528
Single test configurable vacuum leak testing in a benchtop configuration. Features absolute and DP leak testing, auto calibration and adjustable environmental drift correction. Standard test pressure ranges are -14.5, 2, 10, 30, 100, 200, or electronic regulator (PSIG).
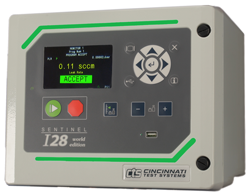
Sentinel I28
Multi-functional, single station vacuum leak detector with a small footprint wall mounting. Features absolute and DP leak testing, easy operator setup and auto calibration. Standard test pressure ranges are -14.5, -2, -0.1 to 4” HG, 0.5, 2, 10, 30, 100, 200, 400, 500, or electronic regulation (PSIG). Specialized testing ranges up to 1000 and 3000 psig are also available.
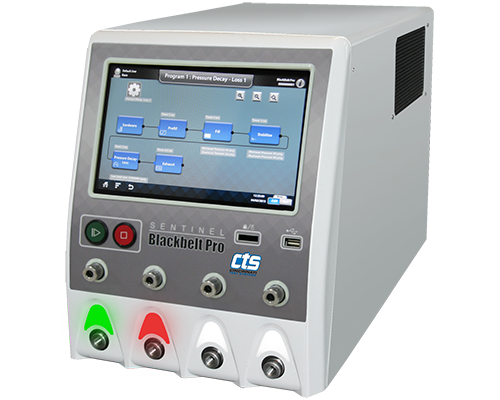
Sentinel Blackbelt Pro
Multi-channel, and multi-functional, 1,2,3,&4 channel vacuum leak detector with a small footprint for benchtop use or industrial wall mounted enclosures. Features easy operator setup and auto calibration. Standard test pressure ranges are -14.5, -2, -0.1 to 4” HG, 0.5, 2, 10, 30, 100, 200, 400, 500, or electronic regulation (PSIG).
Contact Cincinnati Test Systems for Vacuum Leak Testing Systems
Interested in a custom vacuum leak test system? Contact CTS today to learn more or to put our team to work on the vacuum testing unit you need.