Leak Testing Medical Solution, Fluid, or Blood Bags
Compromise isn’t an option with medical device manufacturing. Medical device manufacturing is a highly regulated industry characterized by products with unique, extremely customizable geometries combined with a wide variety of materials – particularly when it comes to blood, solution, and drug management devices. Leak testing are an essential part of the manufacturing process, and CTS has been helping medical device companies maximize product quality with accurate, reliable leak testing solutions for more than 40 years
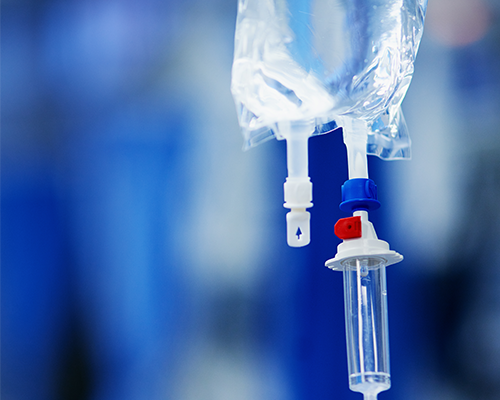
Leak Testing Solution, Drug, and Blood Management Devices
Medical solution and blood bags are typically made from sheets of PVC, EVA, or polyolefin, which are sealed at their perimeter edges and often have tubes or ports exiting the bags interior and sealed between the flat sheets. With complex geometries and materials, the right leak testing partner is especially important.
Testing every bag for leaks is a standard requirement, and automated leaks tests must address the challenges of the flexible material, variable sizes likely being produced, and the manufacturer’s requirements for cycle time and process management. CTS has extensive experience in providing these types of leak test solutions.
For 100% production testing of bags, the most common method uses pressure decay with clean and dry compressed air at positive pressures ranging from 0.1 to 30 psig. The single-channel Sentinel Blackbelt or multi-channel Blackbelt Pro pressure decay instrumentation are designed for this purpose.
Blockage Detection for Cannula and Flow Regulation Devices
Cannula and flow regulation devices are used in thousands of clinical applications, like fluid and drug delivery, precision surgical cuts, medicine administration, precision fluid administration, and much more. These devices provide a pathway for the administration or collection of solutions, blood, and fluids for patients under treatment.
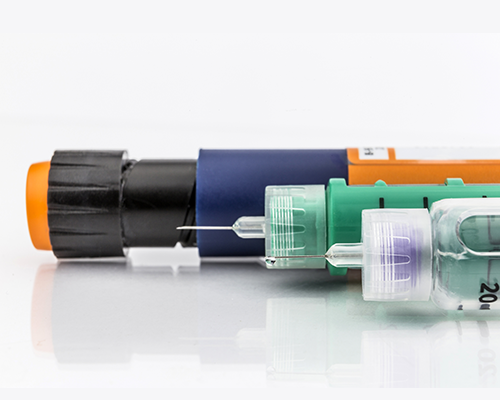
They are often designed to have a nominal expected flow rate with a given media in clinical use. During the manufacturing process, multiple opportunities exist for errors to occur which could alter the intended flow rates enough to adversely affect the person receiving care. These issues are related to the adhesive bonding, extrusion, cut length, and other processes. Testing 100% of devices in production to ensure there are no blockages is critical.
Read the application bulletin to see the typical process to test these devices for blockages or restrictions with a single-channel Sentinel Blackbelt or multi-channel Blackbelt Pro instrument.
Leak Testing Medical Check Valves
Check valves are manufactured in high-speed, high-volume automated production lines that test every single part on the assembly line for potential failures. It’s important to choose accurate and reliable leak testing solutions that won’t slow the process down. Cincinnati Test Systems has decades of experience working in the medical device manufacturing industry, and we understand the details of manufacturing check valves.
Check or one-way valves allow liquid flow in one direction and resist reflux, or back-flow, in the opposite direction based upon the presence of an internal elastomeric “duckbill” valve or an elastomeric disc. This elastomeric valve is often housed in an injection-molded polymer/plastic body which is either ultrasonically welded or adhesively bonded.
There are different tests that can be performed to detect potential part failures:
- Anti-Reflux Valve Leak: verifies the backflow resistance of the one-way valve itself.
- Body Weld Leak: assesses weld or adhesive joint between the two halves for the body for leakage.
- Below Cracking Pressure Valve Leak: challenges the one-way valve to ensure it does not open or leak before it is subjected to a minimum cracking pressure.
- Above Cracking Pressure Valve Opening Verification: checks the one-way valve opens when subjected to a higher pressure than the minimum cracking pressure.
- Actual Cracking Pressure Test: determining the precise cracking pressure for each valve tested.
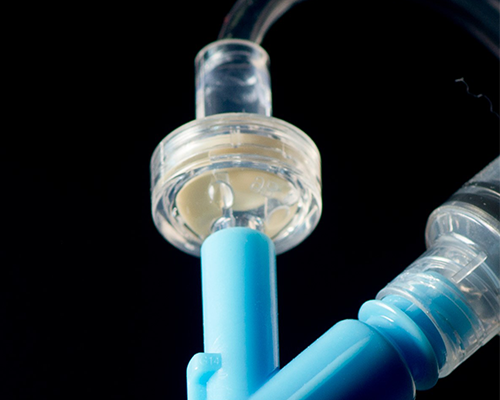
Leak and Blockage Detection for Disposable Tubing Sets
Single-use disposable tubing sets are broadly used in a range of clinical applications for the transfer of IV solutions, drugs/medications, blood, waste, and other various liquids either between containment components or between a container and patient.
In nearly all cases, these tubing sets have both an inlet and one or more outlets which may later be mated by the clinician to any number of various bags/bottles and delivery needles/cannula. While commonly made of plastic material, the temperature resistance of silicone rubber is becoming more popular for these products.
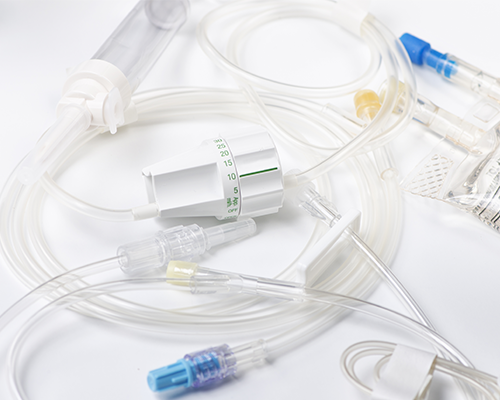
Most tubing sets require testing pressures ranging from 1 psig to 200 psig, with extreme cases at up to 500 psig and beyond. In limited instances, often for wound evacuation applications, are sets that are used clinically under vacuum and are most often tested at vacuum levels between -1 and -12 psig. During assembly where various adhesives or welds mate rigid injection molded components to softer flexible tubing, potential leaks and blockages may occur.
Testing of single-use tubing sets requires a two-step process to detect these issues. A single Blackbelt or Blackbelt Pro instrument can perform both steps.
Our Single-Channel Sentinel Blackbelt or Multi-Channel Blackbelt Pro are the Leak Testing Instruments of Choice for Medical Device Manufacturers.
Leak testing is a critical part of your manufacturing process. Cincinnati Test Systems is a trusted partner to help you reduce cycle time, ensure accuracy, and control product quality.