WHAT IS LEAK TESTING?
Quality assurance is a crucial part of any manufacturing process, and leak testing is a crucial part of quality assurance.
Chapter 1
Industries That Use Leak Testing
Chapter 2
The Various Types of Leak Testing
Chapter 3
The Leak Testing Solutions You Need
Introduction
Quality assurance is a crucial part of any manufacturing process, and leak testing is a crucial part of quality assurance. Every part that contains gas or liquid is going to experience some degree of leakage. But the question isn’t whether the part is going to leak, but rather if the amount of leakage exceeds the acceptable parameters for that specific part.A reliable leak testing process will ensure that products perform as expected, reducing warranty claims and decreasing the cost of rejected parts and units. Leak testing also provides production efficiencies, such as ensuring that supplier components meet quality standards. Testing for part quality increases production efficiency and minimizes rework and scrap waste. Reliable, reproducible leak testing at the start of the manufacturing process also makes for less work needed later on.
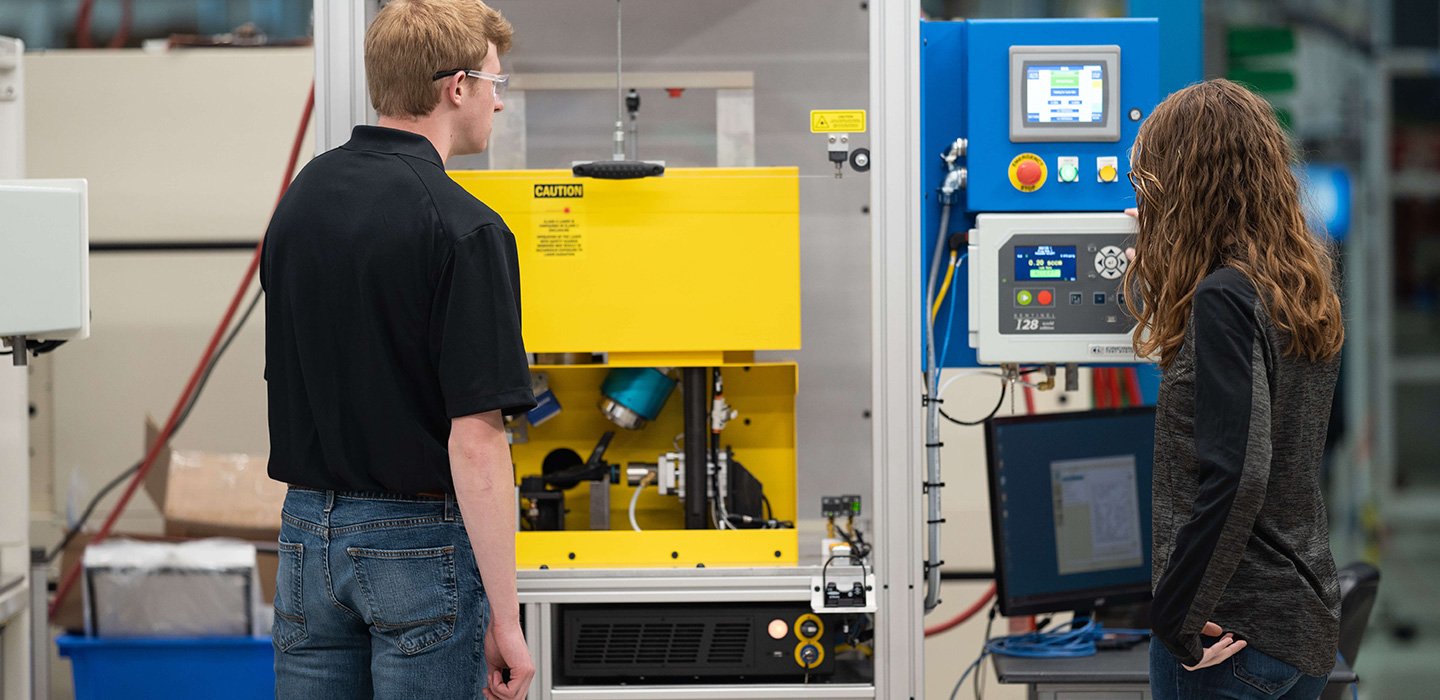
Chapter 1
Industries That Use Leak Testing
Leak testing is an essential part of manufacturing in a variety of industries, including:
- Automotive: Automobile parts, from the engine block to braking and heating systems, have to be tested.
- Electric vehicles: The emergence of electric cars has created new demand for testing EV batteries, their cooling systems, and external sensors for autonomous driving.
- Energy systems: Advances in green energy solutions—such as geothermal, natural gas, biofuels, and fuel cells—require advanced leak testing technology.
- Consumer goods: Power equipment, faucets, appliances, electronic devices, and other consumer products require different forms of leak testing for safety and performance.
- HVAC: Heating and air conditioning systems are made of seals, hoses, and joint fittings, all of which are subject to leakage.
- Medical devices: Tubes, valves, catheters, and other medical devices have to be capable of carrying oxygen, blood, medication, and other fluids.
- Military: Some of the most stringent production guidelines are for military products, and leak testing is used for everything from equipment to chemical munitions.
- Transportation: Everything from scooters to trucks rely on fuel, hydraulic, and pneumatic systems that have to be tested for leaks.
These are just a few industries that rely on leak testing technology from Cincinnati Test Systems (CTS) to verify part and product integrity. CTS is an industry-leading designer and manufacturer of both standard and custom leak test and detection equipment, providing accurate and reliable equipment, instrumentation, and airflow devices to customers around the world.
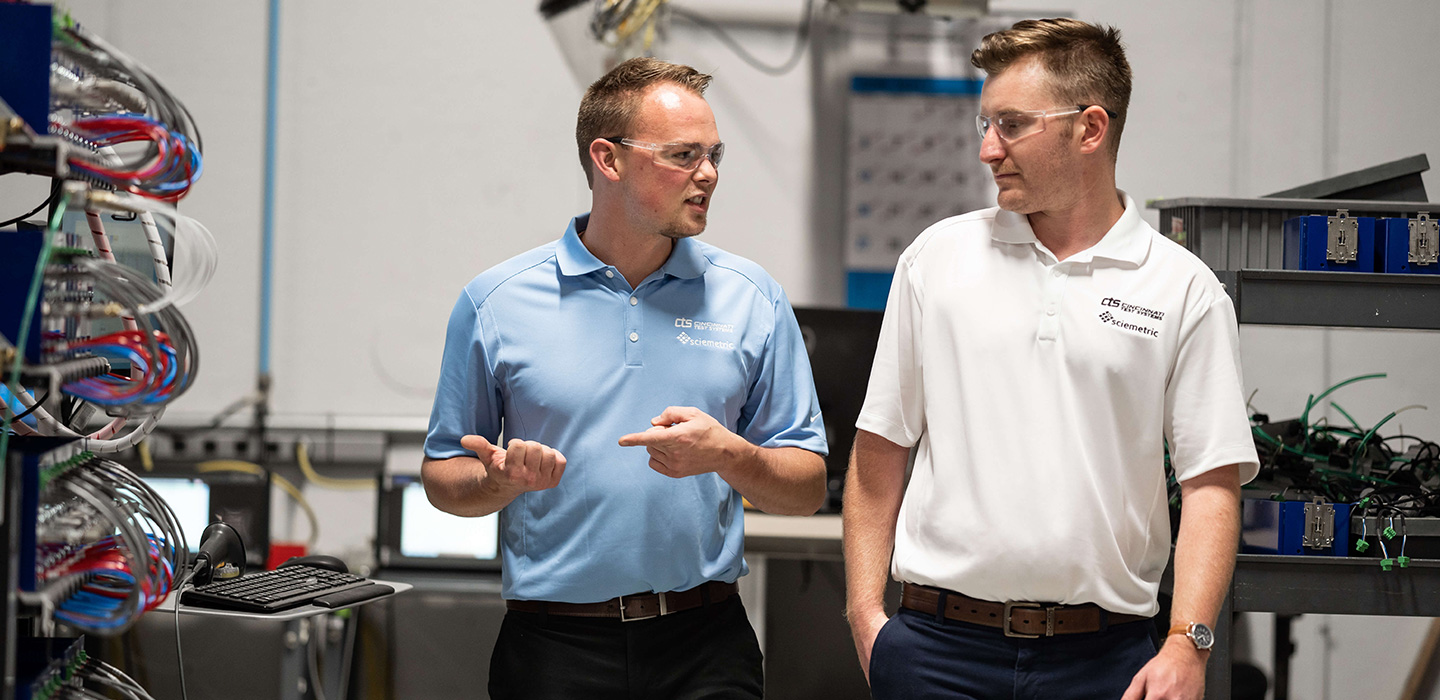
Chapter 2
The Various Types of Leak Testing
Every part or product has unique performance specifications, meaning they all require different types of leak testing. The following is a list of the various types of leak tests and some of their applications:
Pressure Decay and Differential Pressure Decay Leak Tests
Pressure decay testing monitors the internal pressure of a part by filling the part to a predetermined pressure, isolating pressure within the part, then measuring pressure loss to identify any leaks above specification. Similar to a pressure decay test, a differential pressure decay test looks for leaks by measuring the pressure change between a reference volume of air and a test part volume both at the same starting pressure.
Pressure decay testing is sensitive enough to identify non-liquid leaks using either pressure or a vacuum and can be calibrated to measure volumetric flow. It is one of the simplest and most effective forms of leak testing and is used for automotive components, castings, medical devices, and in pharmaceutical manufacturing as part of production and assembly.
CTS products: Sentinel IX5, Sentinel Blackbelt, Sentinel I28, Sentinel 3520
Mass Flow Leak Test
Mass flow leak testing measures the volumetric flow passing through a part or product per unit of time. To test flow, the part is placed under constant, stable pressure and the flow rate is measured against a predetermined leak rate.
Mass flow leak testing is commonly used for high-volume, elastic parts and conducted using gas or liquid. Performing an accurate mass flow test requires tight control of test pressure and environmental factors to minimize noise and ensure repeatability.
CTS products: Sentinel IX5, Sentinel Blackbelt, Sentinel Blackbelt Pro, Sentinel I28, Sentinel 3520
Functional Test
Functional testing measures the performance of complex assemblies. This type of test is conducted by applying force and power to the part to measure output against tolerance and ensure the part is within specifications.
There are various types of functional test systems, including:
- Dunk
- Flow
- Hydrostatic leak
- Fluid and air burst
- Equipment calibration
CTS products: CTS develops custom functional test systems.
Vacuum Leak Test
Even the smallest leaks can have a big impact on part performance, occasionally causing parts to fail or crack. Vacuum leak testing is the most common method of testing sealed parts, as it finds leaks in housings or casings that could be caused by an external source. As a pressure decay test applies pressure, a vacuum is used and a pressure increase is measured based on a leak rate.
Vacuum leak testing is used with underwater sensors or housings, outdoor electrical housings, sealed components, and other components associated with a vacuum source. Compared to pressure decay testing, vacuum leak testing is less sensitive to environmental variables (e.g., temperature change) and takes less time to achieve stable pressure.
CTS products: Sentinel IX5, Sentinel Blackbelt, Sentinel C28WE, Sentinel C20WE, Sentinel I28
Tracer Gas Sniff Leak Test
Tracer gas leak testing is a simple but effective way to find micro leaks outside the range of conventional airflow testing. This type of test provides high sensitivity, accuracy, and repeatability.
Tracer gas has an enhanced resolution for greater test accuracy, the ability to detect micro leaks to 1x10-9 scc/c, and faster test times at low leak rates than airflow leak testing. Test accuracy isn’t affected by temperature and there are significantly fewer false leak failures when trace gas background is adequately controlled.
There are six types of tracer gas tests:
- Helium sniff
- Helium spray
- Helium accumulation
- Nitrogen purge
- Hard vacuum
CTS products: TracerMate II
Tracer Gas Accumulation Leak Test
The tracer gas accumulation test uses the same instrumentation as the atmospheric sniffing test, but uses a chamber to isolate the part under test and contain the tracer gas. Once the tracer gas has accumulated, a mass spectrometer is used to measure the gas leaking from the test part.
The accumulation tracer gas system provides greater accuracy than sniff testing and can detect leaks as small as 1x10-4 scc/s. The test does not require the use of a vacuum chamber and can be loaded manually or automatically. Tracer gas accumulation tests are most effective when the atmospheric background is controlled because atmospheric tracer gas will affect the leak measurement.
CTS products: CTS develops customized accumulation tracer gas systems for customers across a variety of industries.
Hard Vacuum Mass Spectrometer Leak Test
Helium tracer gas is used in several leak tests because it has a small atomic size, so it will pass through extremely small leaks. A hard vacuum test uses vacuum chambers and tracer gas to detect micro leaks. After a stable vacuum is created in the test chamber, a mass spectrometer is used to sample the chamber for helium, continuously analyzing the molecule flow. If the flow exceeds the set reject point, the part fails the leak test.
The hard vacuum helium leak test is the most accurate and efficient of all tracer gas leak tests and is used to test parts with extremely low leak rates, such as sensors, housings, medical devices, sealed components, and refrigeration components.
CTS products: CTS develops customized vacuum leak test systems and other tracer gas equipment for customers across a diverse range of industries.
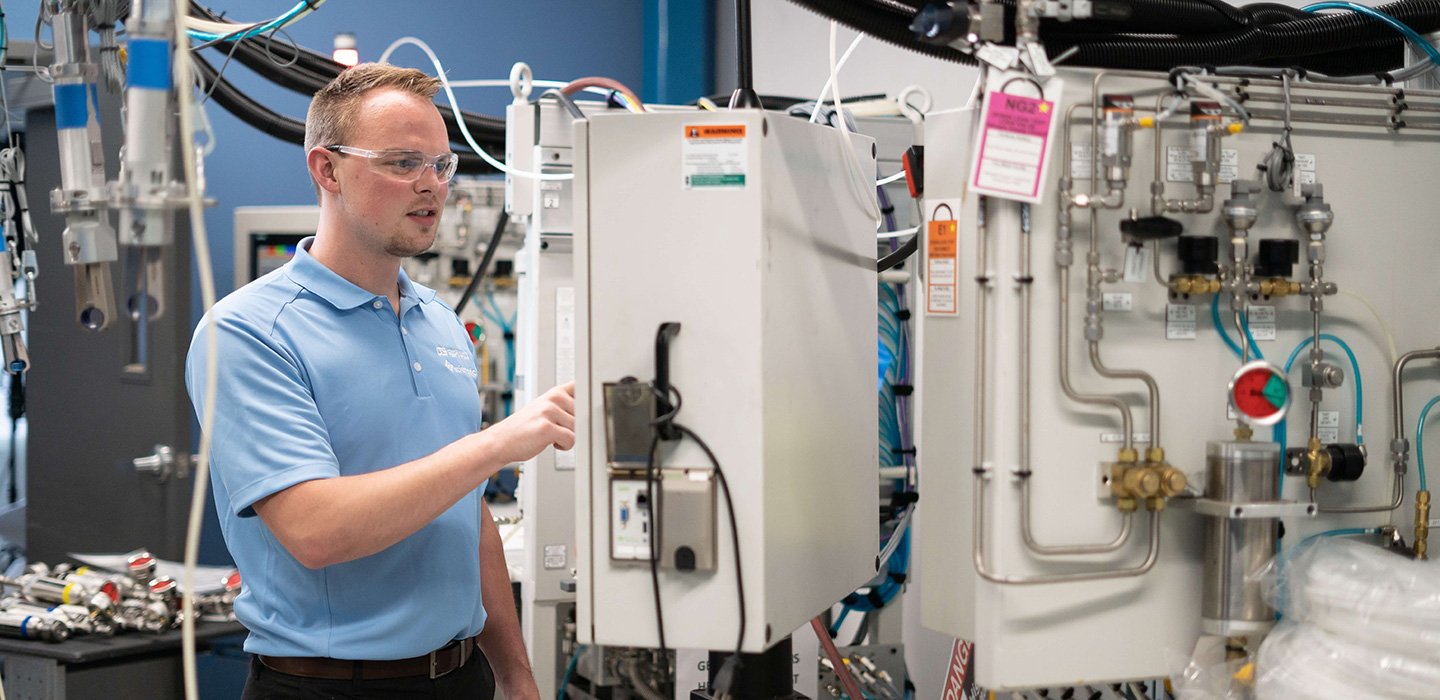
These are just a few of the most common types of leak tests. If you want to learn more about leak testing and potential solutions for your plant or facility, download the Ultimate Guide to Leak Testing for more detailed information. You also can contact the experts at Cincinnati Test Systems to learn more about CTS products and solutions and how they can help you detect leaks.
Download Guide
Leak Testing 101: A Primer
Leak testing is a complex process with variables that can make it difficult to know where and how much your part is leaking. We have taken our decades of experience helping manufacturers find the right leak tests and put together a comprehensive guide on what you need to know, including:
- The most common leak test technologies.
- The basics of leak testing.
- The best type of leak test for your application.
- The pros and cons of leak test technologies.