Hydrostatic Leak Test System
Hydrostatic leak testing is a method of testing a part vessel or cavity for leaks, structural strength, and pressure tightness. It is an internal cavity pressure test that uses a non-compressible pressuring liquid, a volumetric rod-type displacement-sensing device, and a calibrated test instrument to monitor the test pressure for leakage.
How a Hydrostatic Leak Test Works
A calibrated volumetric fill test is commonly used for hydrostatic leak testing. This type of test uses pressure drop to identify the vessel leaks. The process of hydrostatic testing involves filling the vessel with a non-compressible liquid; in most cases water is used. The vessel needs to be completely filled with liquid. System control utilities are provided to allow air to escape and closed before the vessel is pressurized. The test provides time for the pressurized vessel to stabilize before the hydrostatic leak test begins.
This type of system is custom designed to test part design and functionality and commonly used to test vessels that operate with pressure, such as pipe, pipelines, plumbing hydrants, gas cylinders, and boilers to ensure watertight welds, seals, and flow devices meet design specifications, are working properly, and functioning correctly without leaks. The CTS functional test will collect, store, and download data.
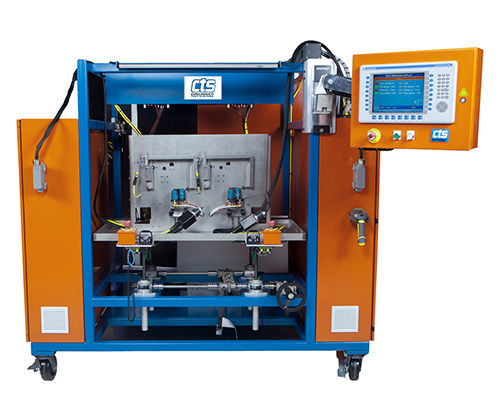
Talk to CTS about Hydrostatic Leak Testing
Cincinnati Test Systems will custom design a hydrostatic test system to test your parts and components testing for: burst, leak, flow, calibration, or integrity testing. These systems can include manual or automatic operation, part load/unload automation, and complete turnkey solution.