Mass Flow Leak Testing
When it comes to testing the integrity of products that are designed to circulate gas or liquid – like engine assemblies, appliances, gas meters, HVAC systems, or some medical devices – measuring leaks and occlusions can present challenges, especially if part variability differs by more than 5-10%. In these cases, mass flow testing is the most accurate and reliable method for determining whether the flow rate falls within the allowable specification for an application. A mass flow leak test:
- Offers instantaneous results
- Operates without destructive testing
- Measures even small leaks
- Accommodates products of varying sizes and flow rates
- Needs no calibration or master part
- Requires steady air pressure
How Mass Flow Leak Testing Works
Mass flow testing defines the rate of flow through a part or device. It involves pressurizing a part and holding pressure constant on that part and measuring how much air is needed to hold the pressure constant. Once the flow pressure has been stabilized, the pressure can be sent through the flow sensor during the test. The flow sensor then measures the leak rate, which is the rate at which air needs to be added to the part to maintain pressure.
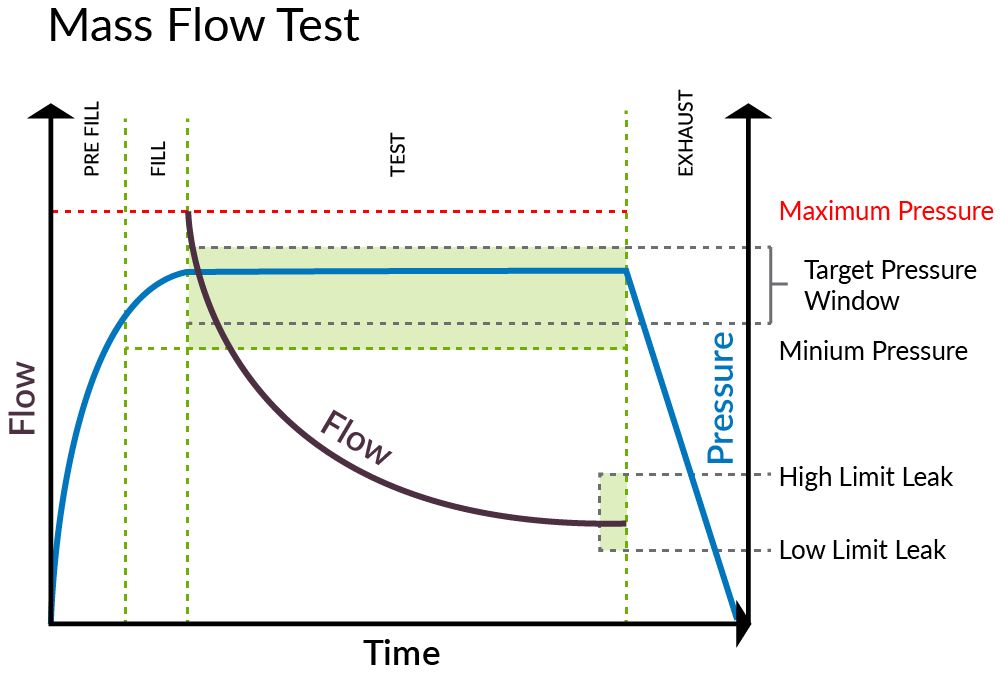
The process is relatively simple.
- Fill the part to test pressure for as long as needed to stabilize. The flow will decrease as the pressure stabilizes.
- When the instrument switches to test, pressure oscillation may be observed until the readings are stable against the target pressure.
- Flow will be measured at the end of the test based on the flow measurement through the flow sensor at that moment.
Success with Mass Flow Testing
It’s important to choose the right leak testing instrumentation for each unique application to ensure accurate measurements. To achieve a reliable mass flow test, a few things are needed.
- Clean air
- Consistent pressure
- Stable test volume (i.e., the part doesn’t expand under pressure)
- Properly scaled flowmeter
When an application demonstrates all four of these, mass flow testing is likely the best option. However, it’s best to talk to an application engineer about the specific application, requirements, and goals.
Download the Free Guide Leak Testing 101: A Primer
Leak testing is a complex process with variables that can make it difficult to know where and how much your part is leaking. We have taken our decades of experience helping manufacturers find the right leak tests and put together a comprehensive digital guide on what you need to know.
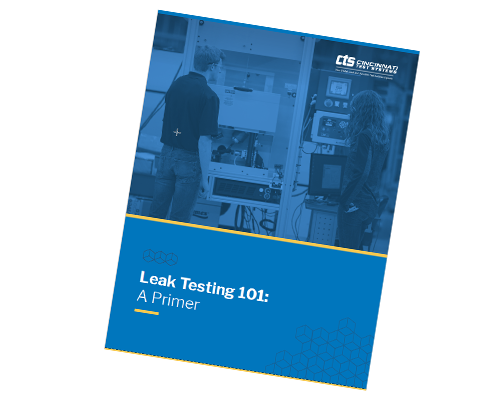
Contact CTS
To Discuss Your Leak Detection System Requirements
Contact CTS
Contact Cincinnati Test Systems to learn more about our leak detection equipment
Contact UsCustomer Login
An account is needed to view restricted documents such as user manuals and to submit RFQ requests.
Sign In