Leak Test Technology, Methods and Equipment
Leak testing is used to determine whether products pass a specified leak limit and meet the desired quality specification. Defects related to leaks can be caused by holes, cracks, weak seals, or permeable areas in a product. They can affect the intended performance of a part, which is why leak testing is one of the most common quality checks performed on production lines.
Cincinnati Test Systems (CTS) designs and manufactures some of the industry’s most technically advanced, best-performing leak test systems, leak testing equipment, gas charge and reclaim handling equipment, and related components and accessories.
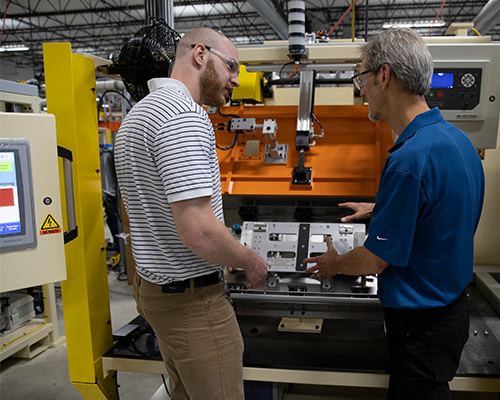
CTS Provides Various Leak Test Equipment Options to Meet Your Requirements
Considerations in selecting a leak testing solution include the size of your component, number of parts being tested, the leak limit, and any surface finishes or hidden internal volumes that might affect the testing. Cincinnati Test Systems offers a broad spectrum of test and reclaim systems, making it easy to find the right one for your unique needs. Our leak test equipment cover various test technologies, including:
Function Test Systems
These function test solutions combine solid engineering with design versatility and provide reliable, repeatable results in numerous function test applications.
Pressure Decay Test Systems
We have pioneered numerous new and innovative technologies for pressure decay testing and offer cost-effective and easy-to-implement solutions for high volume production testing.
Tracer Gas Leak Test Systems
Our leak test devices are the best choice for measurable and repeatable ssc/sec testing in high production environments, regardless of gas or technology used.
Mass Flow Test Systems
CTS offers a range of mass flow test equipment, all of which provide exceptional accuracy and repeatability, and minimize ambient test noise that can skew results.
Pressure Testing Systems
CTS’ pressure testing equipment provides optimal results across a range of testing methods, including hydraulic/hydrostatic testing, occlusion testing, proof testing, and more.
Vacuum Leak Test Systems
Vacuum leak testing is one of the most important leak test methods available. Be sure you’re getting reliable and accurate results with one of CTS’ many high performance vacuum leak test devices.
Leak Test Solutions and Technologies for Effective Leak Detection
Leak testing services are used by a range of industries including eMobility, aerospace, power and energy, industrial, packaging, automotive, medical and pharmaceutical, and more. Several different tools and machines are available for leak detection, with each providing different benefits and levels of sensitivity:
- Bubble or Submersion Testing: A simple gas and air leak detection method where a part or vessel is pressurized, then submerged in water or sprayed with soapy water. Any formation of bubbles indicates that gas or air is escaping. This leak testing method does not provide accurate measurement of the leak but is effective for locating the leak location.
- Hard Vacuum Leak Detection: During this gas leak testing process, parts are placed in a sealed chamber and a vacuum is used to remove all atmosphere. Helium or another gas is then used to fill the part and a sensor in the chamber detects the presence of any leaks. It is highly sensitive and used for detecting both air and gas leaks.
- Helium Accumulation Leak Detecting: This leak testing method is highly sensitive and involves connecting the part to a helium detector, then placing it in an airtight chamber. Pressure is used to create a vacuum effect and if variations in pressure are detected, it indicates that a leak is present.
- Helium Sniff Leak Detection: A highly accurate and sensitive method where helium is used to charge parts to a specified pressure level. Once pressurized, a sniffer device scans the surface to detect leaks. It is effective for air leak testing but might not detect leaks that fall below the testing sensitivity level.
- Pressure Decay Leak Detection: Uses dry, inert gases to measure internal pressure for air leak testing. The part is placed in a vessel that is pressurized to a certain level. The pressure is then monitored for an extended period and if levels drop, it means a leak is present.
- Tracer Gas Leak Detection: This leak testing method is used to detect leaks in water distribution pipes. Tracer gas is injected into the pipe, then a highly sensitive gas detector is used to test the surface above the pipe for gas leaks.
- Ultrasonic Leak Detection: Best suited for detecting larger leaks, this method measures leak rates by measuring the frequency of sound created by a gas or air leak.
- Vacuum Decay Leak Detection: A sensitive leak testing method where parts are vacuum sealed and tested for pressure increases. It provided precise measurements and is not affected by environmental factors such as temperature.
- Helium Spray Leak Detection: Is a two-phase gas leak testing process where parts are first placed in a vacuum sealed vessel to perform initial leak detection. If it passes the first phase, helium is then applied to the part to sense whether there are any gas leaks.